Ongoing Research
Studying experimentally the different aspects of secondary nucleation at different scales ranging from micro to macro.
The analytical tools are tailored for the scale we would like to investigate, i.e. from microfluidic devices, static and dynamic light scattering for the microsclae, all the way up to the in-house built μDISCO for the bigger systems. The μ-DISCO (Dual Imaging System for Crystallization Observation) allows taking stereoscopic images of particles in suspension. The images are processed via image analysis algorithms and machine learning tools to reconstruct the shape of the particles in 3D. Information is then used to generate multi-dimensional particle size and shape distributions (PSSDs).
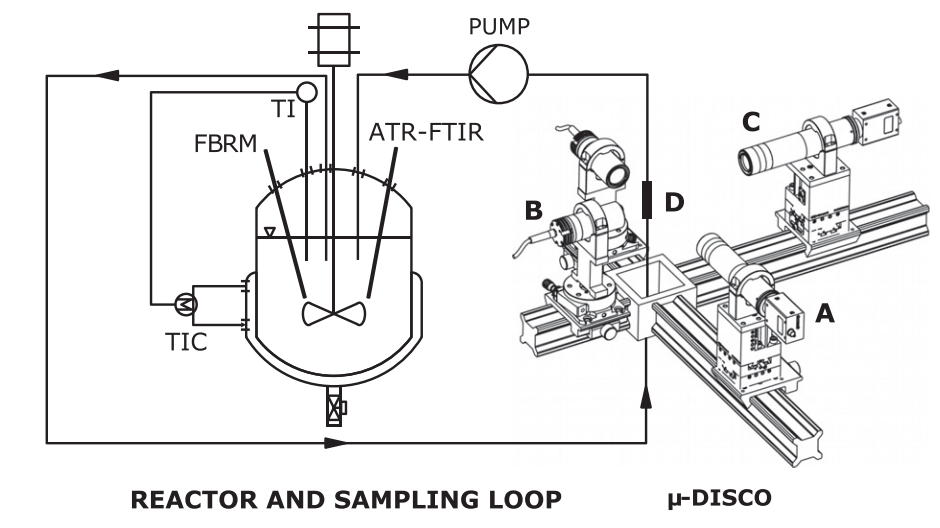
The experiments are coupled with modeling work, where processes are simulated through populatin balance equations (PBE). Phenomena such as primary and secondary nucleation, breakage, growth, dissolution, and agglomeration are taken into account both in batch and continuous systems. The goal is to validate these models with experiments in order to use them in a predictive manner to control and optimize industrial crystalilzation processes.
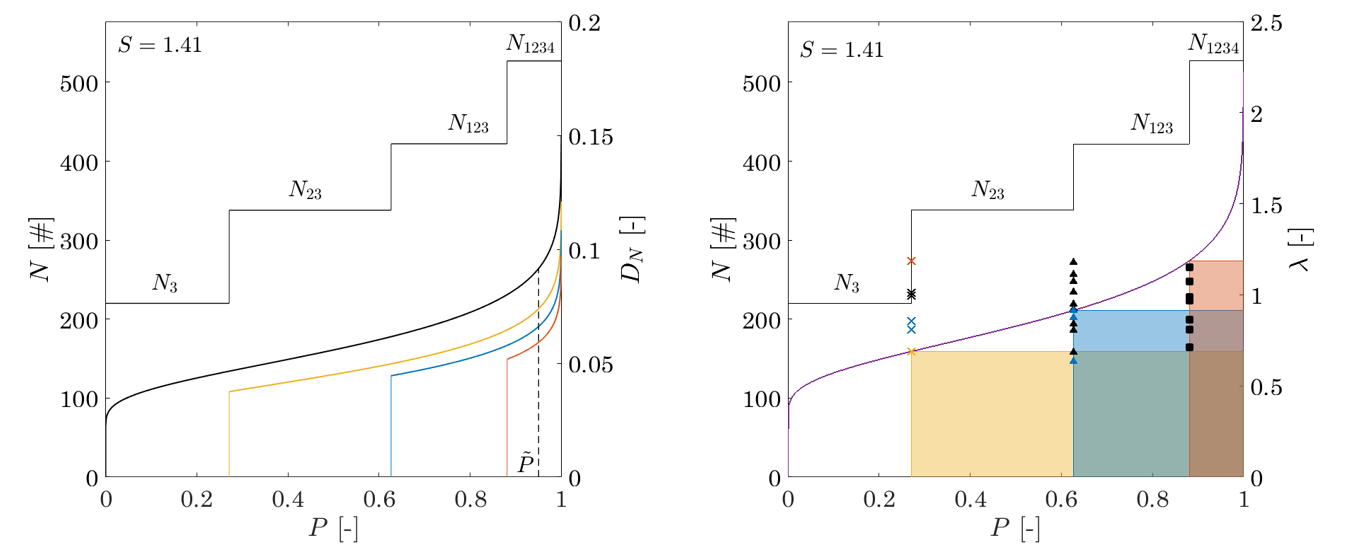
To fully characterize the systems which have been modelled and experimentally studied, computational fluid dynamics (CFD) simulations are essential. The hydrodynamics of the reactors such as shear forces, dissipation rates, velocity fields and mixing have a major influence on the underlying crystallization phenomena, especially when similar time scales are present. Therefore, it is important to have a full understanding of the fluid dynamics and couple it with PBEs.
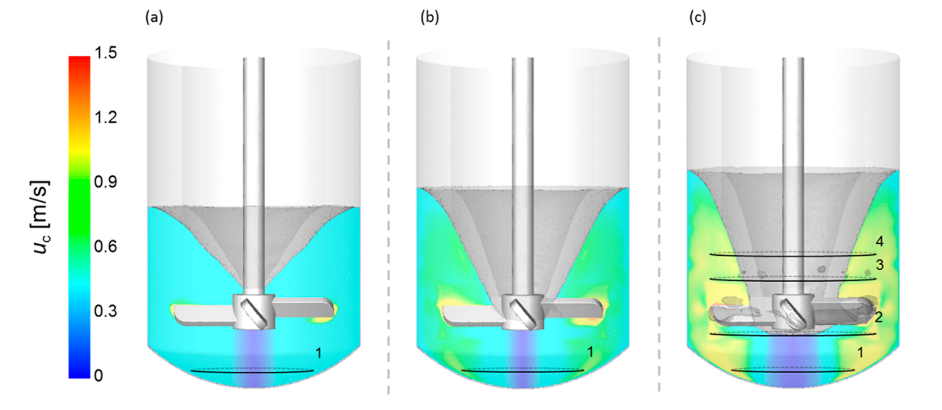